Die Pet Food-Produktion steht vor wachsenden Herausforderungen: steigende Nachfrage, höchste Qualitätsanforderungen und der zunehmende Bedarf an leistungsfähigen Produktionsprozessen. Um diesen Anforderungen gerecht zu werden, wurde eine bestehende Anlage umfassend erweitert und technologisch optimiert. Das Projekt zeigt, wie eine massive Kapazitätserweiterung innerhalb einer bestehenden Gebäudestruktur erfolgreich realisiert werden kann – ohne den laufenden Betrieb zu unterbrechen.
Beschreibung
Mit der Erweiterung und Kapazitätssteigerung einer Produktionsanlage für Pet Food mit einem Auftragsvolumen von weit über 10 Millionen Euro konnte der österreichische Schüttgutspezialist Daxner sein technisches Know-how und Leistungsfähigkeit unter Beweis stellen. Die Arbeiten unter laufendem Betrieb stellten hohe Anforderungen an Planung, Fertigung und Installation. Der international tätige Auftraggeber, ein etablierter Hersteller von Pet Food, wählte daher einen Umsetzungspartner mit umfangreicher Erfahrung im Schüttguthandling, hoher Anpassungsfähigkeit und den notwendigen Ressourcen. Besonders die Integration neuer Systeme in eine bestehende Gebäudestruktur und die hohen Durchsatzleistungen erforderten eine präzise Berechnung und Abstimmung, sowie eine bis ins kleinste Detail durchdachte Vorgehensweise.
Durch die enge Koordination zwischen Auftraggeber und Anlagenbauer entstand eine Produktionslösung, die auf steigende Anforderungen in Kapazität und Qualität ausgelegt ist. Dabei wurden fünf neue Lager-, Förder- und Dosiersysteme in die bestehende Struktur integriert, um eine präzise Verarbeitung unterschiedlicher Futtermischungen unter Einhaltung höchster Hygienevorgaben zu ermöglichen. Groß-, Mittel-, Klein- und Mikrokomponenten werden exakt dosiert, sodass eine gleichbleibend hohe Verarbeitungsqualität sichergestellt ist. Die flexible Projektabwicklung ermöglichte es, laufende Anpassungen effizient umzusetzen und die Prozesse optimal auf neue Rahmenbedingungen des Kunden abzustimmen.
Herausforderungen in Planung und Umsetzung
Die gesamte Planungs- und Abwicklungsphase war von fortlaufenden Anpassungen geprägt. Höchste Anforderungen an die Förderleistung, kurzfristige Änderungen und bauliche Gegebenheiten erforderten ein hohes Maß an Flexibilität. Daxner berücksichtigte jeden Anpassungswunsch und integrierte ihn gezielt in das Konzept.
Besonders die Auslegung der pneumatischen Förderanlagen samt entsprechender Luftaufbereitung (Trocknung und Kühlung) mit einer Förderleistung von bis zu 50 Tonnen pro Stunde stellte eine technische Herausforderung dar. Neben präzisen Berechnungen und einer durchdachten Systemarchitektur musste die Verarbeitung hygroskopischer und temperatursensitiver Rohstoff-Komponenten gewährleistet werden. Gleichzeitig war es aufgrund der globalen Marktpräsenz des Auftraggebers essenziell, dass sämtliche Rezepturen unverändert in höchster Qualität und Sortenreinheit verarbeitet werden. Daher wurde bei allen Komponenten darauf geachtet, Ablagerungen von Rohstoffen zu vermeiden und Maschinen sowie Geräte leicht zugänglich und reinigungsfreundlich zu gestalten. Unter diesem Aspekt wurden alle Komponenten in Hygienic Design inklusive Schnellauszugsvorrichtungen ausgeführt.
Auch die baulichen Rahmenbedingungen spielten eine wesentliche Rolle. Die bestehende Gebäudestruktur musste so integriert werden, dass die laufende Produktion nicht beeinträchtigt wurde. Die ursprünglich angedachte sehr hohe Bauweise machte Anpassungen erforderlich, um massive Fundamentierungskosten zu vermeiden. Daxner setzte auf sein modulares Anlagenkonzept, um die neuen Systeme effizient in die bestehende Infrastruktur einzufügen und eine reibungslose Erweiterung zu gewährleisten.
Technische Struktur und Anlagenintegration
Die erweiterte Anlage umfasst elf Großraumsilos, von denen acht bestehende in das System integriert und drei neu produziert und in die Lager- und Dosiersysteme eingegliedert wurden. Aufgrund der hohen pneumatischen Förderleistung von 50 Tonnen pro Stunde wurden spezielle Maßnahmen zum Verschleißschutz getroffen, darunter der Einsatz hochverschleißfester Rohrbögen und entsprechend dimensionierter Förderrohre. Leistungsfähige Filterabscheider mit Zellenradschleusen und Drehrohrverteilern ermöglichen eine flexible und sortenreine Befüllung der Großkomponentensilos.
Zusätzlich werden 18 Großkomponenten-Silos von den Großraumsilos und Big-Bag-Stationen über pneumatische Fördersysteme befüllt. Die gezielte Aufteilung dieser Komponenten erfolgte unter Berücksichtigung eines durchdachten Explosions-Schutz-Konzeptes. Von den Großkomponenten-Silos werden die Rohstoffe gemäß Rezepturen in Waagen dosiert und anschließend über pneumatische Fördersysteme in die Empfangsbehälter im Mühlenturm gefördert. Somit kann eine mögliche Kreuzkontamination der verschiedenen Rohstoffe auf ein Minimum reduziert werden.
Die Anlage verfügt zudem über fünf Big-Bag-Dosiersysteme, die eine flexible Materialzufuhr ermöglichen – sowohl zur Befüllung der Großkomponentensilos als auch zur direkten Dosierung in die Komponentenwaagen. Ergänzt wird das System durch 25 Kleinkomponenten und 20 Mikrokomponenten. Der hohe Automatisierungsgrad der Dosierung reduziert manuelle Eingriffe auf ein Minimum und gewährleistet eine präzise und nachverfolgbare Rezepturzusammensetzung. Die durchdachte Skalierbarkeit ermöglicht eine flexible Anpassung an neue Rezepturen und Produktionsanforderungen.
Qualitätsmanagement und effiziente Prozesse
Ein entscheidender Erfolgsfaktor war die vorausschauende Abstimmung zwischen allen Projektbeteiligten. Durch eine gezielte Planung und transparente Kommunikation konnten technische Herausforderungen frühzeitig erkannt und effizient gelöst werden. Die enge Zusammenarbeit der Fachabteilungen stellte sicher, dass Anpassungen zeitnah umgesetzt wurden, ohne die Produktionsziele des Auftraggebers zu beeinträchtigen.
Neben einer durchdachten Planung spielte auch die Fertigungsqualität der Anlagenkomponenten eine zentrale Rolle. Die Produktion erfolgte überwiegend im firmeneigenen Werk in Österreich, wodurch gleichbleibend hohe Verarbeitungsstandards sichergestellt wurden. Die Kombination aus technologischem Know-how und präziser Umsetzung schuf eine zuverlässige Produktionslösung, ausgeführt komplett in Hygienic Design, mit hoher Leistungsfähigkeit und Langlebigkeit.
Fazit: Zukunftsfähige Technologie mit nachhaltigem Mehrwert
Das Projekt verdeutlicht, wie gezielte technologische Weiterentwicklung und eine durchdachte Planung eine leistungsfähige Produktionslösung schaffen. Daxner hat nicht nur eine maßgeschneiderte Anlagenerweiterung realisiert, sondern eine solide Basis für zukünftige Produktionssteigerungen gelegt.
Dank moderner Technik und flexibler Strukturen kann der Auftraggeber auf Marktveränderungen rasch reagieren und seine Prozesse effizient weiterentwickeln. Die Erweiterung ermöglicht eine nachhaltige Optimierung der Pet Food-Produktion und sichert die langfristige Wettbewerbsfähigkeit des Unternehmens.
Schlüsselkomponenten
dieser Lösung
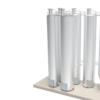
Silos & Austragen
- Segment-/Trogkettenförderer
- Düsenfilter als Siloaufsatzfilter
- Düsenfilter
- Magnet-Separatoren
- Dosierschnecken
- Sackaufschüttung
- Schleusen
- Rohrweichen und Zubehör
- Pneumatische Druck- und Saugförderanlagen
- Trogförderschnecke
- Rohrförderschnecken | Dosierschnecken
- Big-Bag Entleerstation kombiniert mit Sackaufgabesystem
- Big-Bag Befüllsystem Eco Basic
- Vibroaustragboden
- Außensilos | Lagersilos
- Innensilos | Tagessilos
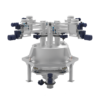
Dosieren & Verwiegen
- Düsenfilter
- Magnet-Separatoren
- Behälterwaage
- Dosierschnecken
- Mittel- und Kleinkomponentendosiersysteme
- Manuelle Dosiersysteme für Klein- und Kleinstkomponenten
- Sackaufschüttung und Kontrollsiebmaschine VIB & PRESS
- Sackaufschüttung
- Schleusen
- Rohrförderschnecken | Dosierschnecken
- Vibroaustragboden
- Rührwerkaustragapparat
- Innensilos | Tagessilos
Sie sind interessiert?
Lassen Sie uns reden.
Senden Sie uns Ihre Kontaktdaten und einer unserer technischen Verkaufsmitarbeiter meldet sich bei Ihnen um Ihr Projekt zu besprechen oder finden Sie einen DAXNER Partner in Ihrer Nähe.