The challenges of pet food manufacturing are increasing: rising demand, strict quality standards, and growing requirements for high-performance production processes. To meet these demands, an existing facility was extensively expanded and technologically upgraded. This project demonstrates how a significant capacity increase can be successfully realized within an existing building structure—without interrupting ongoing operations.
Description
When a pet food production plant set out to expand their operation and increase production capacities (an investment representing well over 10 million euros), Austrian bulk material specialist Daxner showcased its technical expertise and performance capabilities. Executing the project during live operations posed high demands on planning, fabrication, and installation. Given their international operations, this established pet food manufacturer selected a partner with the following: proven experience in bulk material handling, a high level of adaptability, and the necessary resources. Integrating new systems within the existing infrastructure while maintaining the existing production rates required precise calculations and coordination, along with a meticulously planned execution strategy.
Thanks to close collaboration between the client and the system integrator, a production solution was developed that meets their growing demands for both capacity and quality. Five new systems for storage, conveying, and dosing were integrated into the existing facility to enable precise processing of various feed blends while maintaining the highest hygiene standards. Whether bulk, major, minor, or micro components, all are dosed with pinpoint accuracy, ensuring consistently high processing quality. The flexible project execution enabled efficient implementation of ongoing adjustments and allowed processes to be fine-tuned to the client’s evolving needs.
Challenges in Planning and Execution
The planning and implementation phases were characterized by continuous adaptations. High requirements for conveying capacity, short-term changes, and structural constraints demanded a great deal of flexibility. Daxner addressed every adjustment request and skillfully incorporated it into the concept.
One of the key technical challenges involved designing pneumatic conveying systems with a throughput capacity of up to 50 tons per hour while maintaining drying and cooling for process air throughout the system. In addition to precise calculations and well-planned system architecture, hygroscopic and temperature-sensitive raw materials had handled with greatest care. Given the client’s global market presence, it was critical that all formulations be processed with uncompromising quality and batch purity. To support this, all system components were designed to prevent material build-up and ensure easy accessibility and cleanability of equipment. Every new system element was implemented in hygienic design, including mechanisms for quick changeovers.
Structural conditions also played a crucial role. The existing building structure had to be integrated in a way that did not disrupt ongoing production. The originally planned construction would have led to substantial foundation costs due to height, prompting a design change. Daxner applied its modular system concept to efficiently embed the new systems into the existing infrastructure and ensure a seamless expansion.
System Design and Technical Integration
The expanded facility now includes eleven large-capacity (bulk) silos—eight of which were existing units integrated into the system, while three new bulk silos were manufactured and incorporated into the storage and dosing systems. Due to the high pneumatic conveying capacity of 50 tons per hour, specific wear-protection measures were implemented, including the use of highly wear-resistant pipe bends and appropriately sized conveying lines. High-performance filter separators with rotary valves and diverter tubes enable flexible and contamination-free filling of major component silos (day bins).
Additionally, 18 major component silos are fed via pneumatic conveying systems from both the bulk silos and bulk bag (super sack) unload stations. Component allocation was carefully planned as part of an explosion-protection concept. From the major component silos, raw materials are dosed into scales according to specific recipes and conveyed via pneumatic lines to the receiving hoppers in the milling tower—minimizing any risk of cross-contamination.
The facility also includes five bulk bag (super sack) dosing stations, allowing for flexible material input—either into the major component day silos or directly into the component scales. The system is further complemented by 25 minor and 20 micro components. A high degree of automation in the dosing process minimizes manual intervention and ensures precise, traceable formulation composition. The system’s smart scalability enables rapid adaptation to new recipes and production requirements.
Quality Management and Efficient Processes
One of the key success factors was the proactive coordination among all project stakeholders. Through targeted planning and transparent communication, technical challenges were identified early and resolved efficiently. The close collaboration between departments ensured that adjustments could be implemented without jeopardizing the client’s production targets.
In addition to thoughtful planning, the quality of the plant’s new equipment also played a central role. Most of the production was carried out at Daxner’s in-house facility in Austria, ensuring consistently high manufacturing standards. The combination of technological expertise and precise execution resulted in a robust production solution—entirely implemented in hygienic design—delivering high performance and long-term durability.
Conclusion: Future-Proof Technology with Sustainable Value
This project is a compelling example of how targeted technological development and smart planning can create a powerful production solution. Daxner not only delivered a customized plant expansion but also laid a solid foundation for future capacity growth.
Thanks to innovative technology and flexible system structures, the client is now well-positioned to respond quickly to market changes and continue optimizing production processes efficiently. The expansion ensures a sustainable upgrade to pet food manufacturing while strengthening the company’s long-term competitiveness.
Key components
for this solution
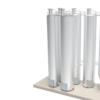
Silos & discharge
- Chain conveyors
- Jet filter
- Jet bin vent filter
- Magnet separators
- Dosing screw conveyors
- Rotary valves
- Bag intake station
- Diverter valves and accessories
- Pneumatic pressure and vacuum conveying systems
- Trough screw conveyors
- Tubular screw conveyors | Dosing screw conveyors
- Combined bag dump & big bag discharge station
- Big bag loading system Eco Basic
- Vibro bin discharger
- Outdoor silos | Storage silos
- Indoor silos | Day silos
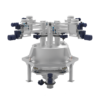
Dosing & Weighing
- Jet filter
- Magnet separators
- Weighing bin
- Dosing screw conveyors
- Dosing systems for medium and small batches
- Manual dosing system for small and micro batches
- Bag intake & screening machine VIB & PRESS
- Bag intake station
- Rotary valves
- Tubular screw conveyors | Dosing screw conveyors
- Vibro bin discharger
- Rotary bin discharger
- Indoor silos | Day silos
Sounds interesting?
Let us know.
Send us your inquiry and a technical sales person is calling you back to talk about your projects or find a DAXNER partner company around you.